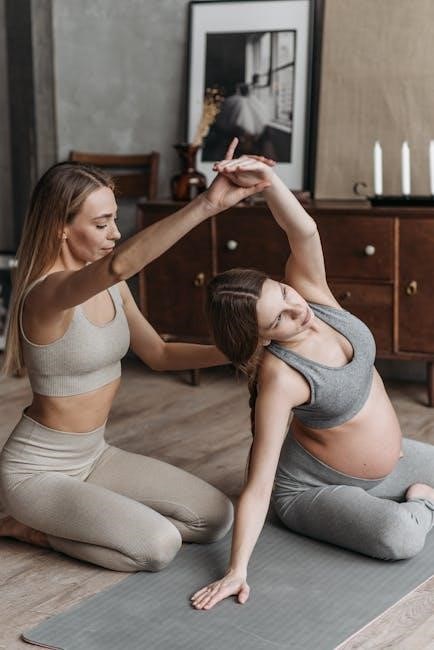
Manual handling training is essential for workplace safety, reducing injuries, and enhancing productivity. The Train the Trainer model empowers experts to effectively instruct others, ensuring proper techniques are adopted universally.
1.1 Importance of Manual Handling Training
Manual handling training is crucial for preventing workplace injuries, reducing absenteeism, and promoting a safety-first culture. It equips employees with skills to handle tasks safely, minimizing the risk of musculoskeletal disorders. Proper training ensures compliance with legal and regulatory standards, protecting both employers and employees from potential liabilities. By fostering a safer work environment, it enhances productivity and employee morale. Organizations that prioritize manual handling training demonstrate a commitment to worker well-being, which can lead to reduced costs associated with workplace accidents and improved overall efficiency. Effective training also empowers employees to recognize hazards and adopt best practices, creating a sustainable safety-conscious workforce.
1.2 Overview of the Train the Trainer Concept
The Train the Trainer concept is a structured approach where experienced individuals are equipped to deliver manual handling training effectively. This method ensures that knowledge and skills are transferred consistently across an organization. Trainers are taught how to design engaging sessions, demonstrate techniques, and assess competence. The model promotes scalability, allowing companies to maintain high training standards without external resources. By empowering trainers, the concept fosters a culture of safety and continuous improvement. It also ensures that training aligns with legal requirements and organizational goals. This approach is cost-effective and sustainable, enabling businesses to build internal expertise and adapt training to specific workplace needs.
Key Components of Manual Handling Training
Manual handling training focuses on legal compliance, risk assessment, and proper lifting techniques to ensure workplace safety and reduce injury risks effectively.
2.1 Legal and Regulatory Requirements
Manual handling training must comply with legal standards to ensure workplace safety. Employers are legally required to assess manual handling risks and provide adequate training. Regulations, such as the Manual Handling Operations Regulations 1992, mandate employers to reduce risks through proper training and equipment. Employees must also follow safety protocols to prevent injuries. Trainers play a crucial role in ensuring compliance by educating workers on legal obligations and safe practices. Non-compliance can result in legal penalties, highlighting the importance of thorough training programs. Understanding these regulations is essential for creating effective training that protects both employees and employers, fostering a safer work environment.
2.2 Risk Assessment and Hazard Identification
Risk assessment and hazard identification are critical components of manual handling training. Trainers must teach participants to identify tasks involving manual handling and evaluate associated risks. This process involves analyzing tasks, work environments, and individual capabilities to pinpoint potential hazards. Common hazards include heavy loads, awkward postures, and repetitive movements. Conducting regular risk assessments ensures that unsafe practices are addressed promptly. Trainers should emphasize systematic approaches, such as using checklists or observation techniques, to identify and prioritize risks. By understanding how to assess and mitigate hazards, trainees can significantly reduce the likelihood of injuries. This step is fundamental in creating a safer and more efficient workplace environment.
2.3 Proper Lifting Techniques and Ergonomics
Proper lifting techniques and ergonomics are fundamental to manual handling training. Trainers should emphasize maintaining a neutral spine, bending at the knees, and keeping loads close to the body. Participants should learn to avoid twisting and instead pivot with their feet. Ergonomic principles, such as adjusting workstations and using assistive equipment, are essential to reduce strain. Demonstrating correct postures and movements helps trainees adopt safe practices. Practical exercises allow trainees to apply these techniques, ensuring they understand how to minimize physical stress. By mastering proper lifting and ergonomic strategies, workers can significantly reduce the risk of injury and improve overall efficiency in their tasks.
Delivering Effective Manual Handling Training
Effective manual handling training engages participants through interactive sessions, practical demonstrations, and real-world examples. Encouraging active participation and feedback ensures trainees grasp and apply safe handling techniques confidently.
3.1 Creating Engaging and Interactive Sessions
Creating engaging and interactive sessions is crucial for effective manual handling training. Incorporate hands-on exercises, group activities, and real-life scenarios to make learning practical and relatable. Use visual aids like videos and demonstrations to enhance understanding. Encourage participation through open discussions and feedback loops, ensuring trainees feel involved. Integrate quizzes and role-playing to maintain attention and test knowledge retention; Personalized learning experiences, such as tailored exercises based on job roles, can also boost engagement. By fostering an interactive environment, trainers can ensure that trainees not only understand but also apply safe manual handling techniques confidently in their daily tasks.
3.2 Using Visual Aids and Practical Demonstrations
Visual aids and practical demonstrations are vital for effective manual handling training. Videos, images, and infographics can simplify complex techniques, making them easier to understand. Live demonstrations allow trainees to observe proper lifting methods and ergonomics in action. Hands-on practice enables trainees to apply what they’ve learned, with trainers providing immediate feedback. Combining visual and practical elements helps reinforce learning, ensuring trainees retain information better. This approach also caters to different learning styles, making sessions more inclusive. By using real-world examples, trainers can illustrate how manual handling techniques apply in various workplace scenarios, reducing the risk of injuries and improving overall safety standards.
3.3 Encouraging Active Participation and Feedback
Active participation and feedback are crucial for effective manual handling training. Trainers should encourage trainees to engage through group discussions, role-playing, and hands-on exercises. This fosters a collaborative learning environment and helps trainees apply theoretical knowledge practically. Immediate feedback from trainers and peers enhances understanding and corrects improper techniques. Incorporating surveys or Q&A sessions allows trainees to voice concerns and clarify doubts. Feedback loops ensure continuous improvement, making training more relevant and impactful. By promoting engagement, trainers can identify knowledge gaps and tailor sessions to meet specific needs, ultimately improving overall learning outcomes and workplace safety standards.
Assessing Trainee Competency
Assessing trainee competency involves evaluating understanding and practical skills through tests, practical exams, and demonstrations. Feedback ensures proper techniques are applied safely and effectively in real-world scenarios.
4.1 Methods for Evaluating Understanding and Skills
Evaluating trainees involves a mix of theoretical and practical assessments. Written tests or quizzes can gauge knowledge retention, while practical demonstrations ensure proper lifting techniques. Observational checklists allow trainers to assess real-time task performance, ensuring adherence to safety protocols. Feedback sessions and skill competitions can further validate competency. These methods provide a comprehensive understanding of trainees’ abilities, helping identify areas for improvement. Continuous assessment ensures that manual handling skills are applied consistently and safely in workplace environments, reducing injury risks and promoting a culture of safety.
4.2 Providing Constructive Feedback and Coaching
Constructive feedback is crucial for improving trainees’ manual handling skills. Trainers should focus on specific observations, providing clear examples of what was done well and areas for improvement. Using a positive tone encourages learning and reduces defensiveness. Practical demonstrations paired with feedback help trainees understand and correct their techniques. Breaking down complex tasks into smaller steps allows for targeted coaching. Encouraging questions and open dialogue fosters a supportive learning environment. Follow-up sessions ensure sustained improvement and reinforce safe practices. Effective coaching not only enhances technical skills but also builds confidence, leading to safer and more efficient manual handling practices in the workplace.
Real-World Applications of Manual Handling Training
Manual handling training is applied across industries like healthcare, manufacturing, and logistics, ensuring safe load handling, reducing workplace injuries, and improving operational efficiency through proper techniques.
5.1 Industry-Specific Case Studies
Industry-specific case studies highlight the practical benefits of manual handling training. For instance, in healthcare, training has significantly reduced injuries among nurses handling patients. In manufacturing, implementing proper lifting techniques decreased workplace accidents by 30%. Logistics companies report improved efficiency and fewer worker compensation claims. These real-world examples demonstrate how tailored training programs address unique challenges in each sector. By analyzing these case studies, organizations can adopt best practices, ensuring safer and more productive environments. The Train the Trainer model plays a crucial role in sustaining these improvements, as trained instructors can adapt strategies to meet industry needs. Such examples underscore the value of manual handling training in diverse workplace settings.
5.2 Addressing Common Challenges and Misconceptions
A common misconception is that manual handling depends solely on physical strength, while proper techniques are more crucial for preventing injuries. Trainers face challenges like employee resistance, with workers often doubting the necessity of training. To address this, engaging and interactive sessions using real-life examples can enhance relevance and participation. Additionally, maintaining training standards over time is essential, as complacency can lead to poor practices. Regular refresher courses and continuous feedback help reinforce proper techniques and ensure sustained competency. By understanding these challenges and implementing effective strategies, trainers can significantly enhance the effectiveness and long-term impact of manual handling training programs effectively.
Continuous Improvement and Refresher Training
Continuous improvement ensures manual handling training stays updated with new techniques and industry standards, while refresher courses prevent skill fade and maintain workplace safety through regular assessments.
6.1 The Role of Refresher Courses in Maintaining Standards
Refresher courses play a crucial role in maintaining high standards of manual handling training. They ensure that trainers and employees remain updated on the latest techniques, regulations, and best practices. Over time, skill fade can occur, making regular refreshers essential to reinforce proper lifting methods and ergonomic principles. These courses also address any gaps in knowledge or adherence to safety protocols, helping to sustain a culture of safety within the workplace. By periodically revisiting key concepts, refresher training not only prevents accidents but also aligns with evolving industry standards and legislative requirements, ensuring continuous improvement and accountability in manual handling practices.
6.2 Incorporating New Techniques and Updates
Incorporating new techniques and updates is vital for keeping manual handling training relevant and effective. As industry practices evolve, trainers must stay informed about advancements in ergonomics, lifting methods, and safety technologies. Regular updates ensure that training content reflects current best practices, addressing emerging challenges and improving trainee outcomes. Trainers can source updates through workshops, webinars, and industry publications, ensuring they impart the latest knowledge. By integrating new techniques, such as digital tools for risk assessment or innovative lifting aids, training programs remain engaging and practical. This continuous improvement not only enhances trainee competency but also aligns with changing workplace demands, fostering a safer and more efficient work environment.
The Future of Manual Handling Training
The future of manual handling training lies in integrating advanced technologies like VR and AI to create immersive, data-driven learning experiences, enhancing safety and efficiency.
7.1 Leveraging Technology for Enhanced Learning
Technology is revolutionizing manual handling training by offering innovative tools that enhance engagement and understanding. Virtual reality (VR) and augmented reality (AR) provide immersive simulations, allowing trainees to practice lifting techniques in a risk-free environment. Interactive e-learning platforms and mobile apps enable flexible learning, while data analytics track progress and identify areas for improvement. AI-driven systems can offer personalized feedback, ensuring trainees master proper techniques. Additionally, video demonstrations and 3D models help visualize complex movements, making training more accessible and effective. These advancements not only improve knowledge retention but also reduce workplace injuries, creating a safer and more efficient learning experience for all participants.
7.2 Adapting to Changing Workplace Dynamics
As workplaces evolve, manual handling training must adapt to new challenges and opportunities. With advancements in technology and shifting workforce demographics, trainers need to incorporate diverse tools and techniques. Personalized training approaches can cater to varying physical abilities and learning styles. Flexibility in training delivery, such as online or hybrid models, accommodates different work environments. Continuous updates to training programs ensure they align with industry advancements and new regulations; Promoting a safety culture and open communication encourages ongoing improvement in manual handling practices. By staying informed and proactive, trainers can effectively address the changing dynamics, ensuring a safe and efficient work environment for all.